When it comes to building lab furniture, there are only a few options. Most people will think it should be built with MDF boards or similar engineered wood, but that’s not good for a laboratory environment. Similar goes for stainless steel. The absolutely best way to build a lab furniture like a lab workbench is to use CRCA material. At least, CRCA steel gives the best balance between cost and usability.
But what is CRCA steel anyway, do you know? Well, today we will talk about CRCA full form, CRCA sheet material, how CRCA steel is made, quality of CRCA steel, and why CRCA steel is best for lab furniture manufacturing. So, let’s just jump into it.
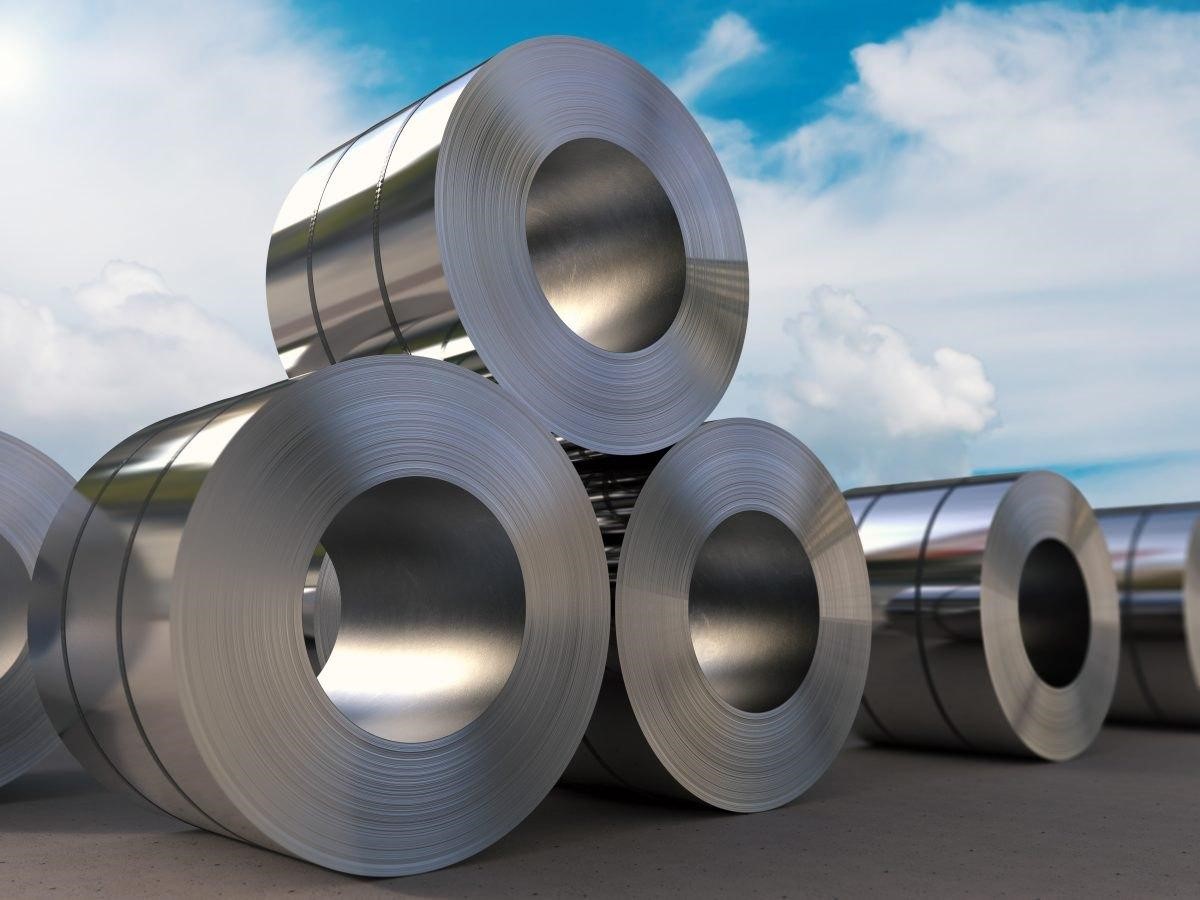
What is CRCA?
CRCA is an abbreviation, whose full form is “Cold Rolled Close Annealed”. This is a special type of treatment on steel at the end of the processing queue, which gives the steel some special properties like additional strength and durability. The name comes from two processing stages of the steel ‒ cold-rolling it into sheet form, and then annealing it in a closed container without the presence of air.
CRCA sheets are the sheet metal, kept in huge rolls, that come out of this process. It can also be cut in 3-7 meter long pieces and stored.
How CRCA Sheet are Manufactured
As we generally know, we commonly shape metal by heating it and therefore softening it up. The same comes in effect when you need to thin out a large block of steel into thin plates. You heat it up till it glows, and then pass it through a couple of rollers that press the softened metal into thin plates.
However, with standard steel, there is a problem with this method. When the thinned material cools, not all parts of it are cooled completely equally. That creates strain in the final sheet and forms various irregularities on the surface of the sheet like pits and bumps.
For large scale applications, this may not be an issue. You won’t need to worry about factory finishes when you are building things like a bridge or something ‒ you’ll do it later by hand. However, what if you don’t need plates but very thin sheets, like, just a millimeter thick? In that case, the surface quality of the sheet matters a lot, since you cannot smooth it over later. Also, you will need a lot of strength from that thin piece of metal to hold the weight of your stuff. How to achieve this?
This is where the method of cold-rolling comes in. It’s not done directly ‒ instead, first they hot-roll the steel to reduce its thickness to some extent in the traditional way. This creates thick sheets of irregular surface from steel ingots. Then, after they have cooled off to room temperature, they are passed through very strong rollers again ‒ this time with a very little gap between the rollers. This compresses the steel into very thin sheets of intended thickness, which are then collected into rolls or coils.
<image alt= “CRCA Steel is cold rolled” title= “Hot rolling vs cold rolling process for CRCA”>
However, this process has a problem. When the cold rollers compress the steel, any irregularities and tensions that came in the original get compressed too. Which means that the final sheet will be very strong, but hard and brittle like iron is. We don’t want that!
And that is what close-annealing is supposed to fix. They put the rolls of cold-rolled steel into a bell furnace and cook them for a very long time (usually 2-3 days) at around seven hundred degrees centigrade. Actually the heating process is fast enough, but it is cooled over a long period by controlling the temperature. Additionally, the bell furnace is airtight and filled with some sort of non-oxidizing gas, like nitrogen.
So, what does close annealing do to the steel? First of all, it softens the material, making it non-brittle. That means the final CRCA sheet will bend rather than break. Secondly, it increases ductility of the steel, which helps a lot when drawing it. The close annealing process also improves other physical properties of the sheet, like strain hardening coefficient and planar anisotropy. All in all, it makes the sheets stronger and more durable.
Technically, this should be the end of the manufacturing process of CRCA steel. But in real factories there is another step. The CRCA coils are oiled first to prevent it from rusting, and then sold or stored as necessary. In case of lab furniture manufacturing, the steel is sprayed with an anti-corrosive, anti-rust coating (which also creates the color of the material).
Quality of CRCA Sheet
CRCA Steel is excellent for mass production of furniture and machinery parts due to its high strength and ease of production. It is suitable for quick and easy prefabrication and installation, and has very fine and smooth surfaces suited for any finish. You wouldn’t need formwork to handle CRCA steel and it changes little due to temperature too, making it very reliable. Not to mention, unlike MDF boards it is fireproof, termite-proof, and obviously does not rot. With a good anti-corrosive coating, it can withstand a lot of environmental damage as well.
CRCA Steel IS Specification Sheet
According to IS:513, a proper CRCA sheet should have the following quality specifications:
- Thickness ‒ 0.3 mm to 5.5 mm
- Thickness tolerance ‒ 0.02 mm
- Width of sheet ‒ 6 mm to 1000 mm
- Sheet length ‒ up to 7000 mm
- Temper ‒ full hard, ½ hard, ¼ hard, ⅛ hard
- Surface finish ‒ matt, dull, bright, mirror
- Grade ‒ D/DD/EDD, Super EDD
- Edge finish ‒ mill or slit
- Camber tolerance ‒ 1.5 mm per 1000 mm
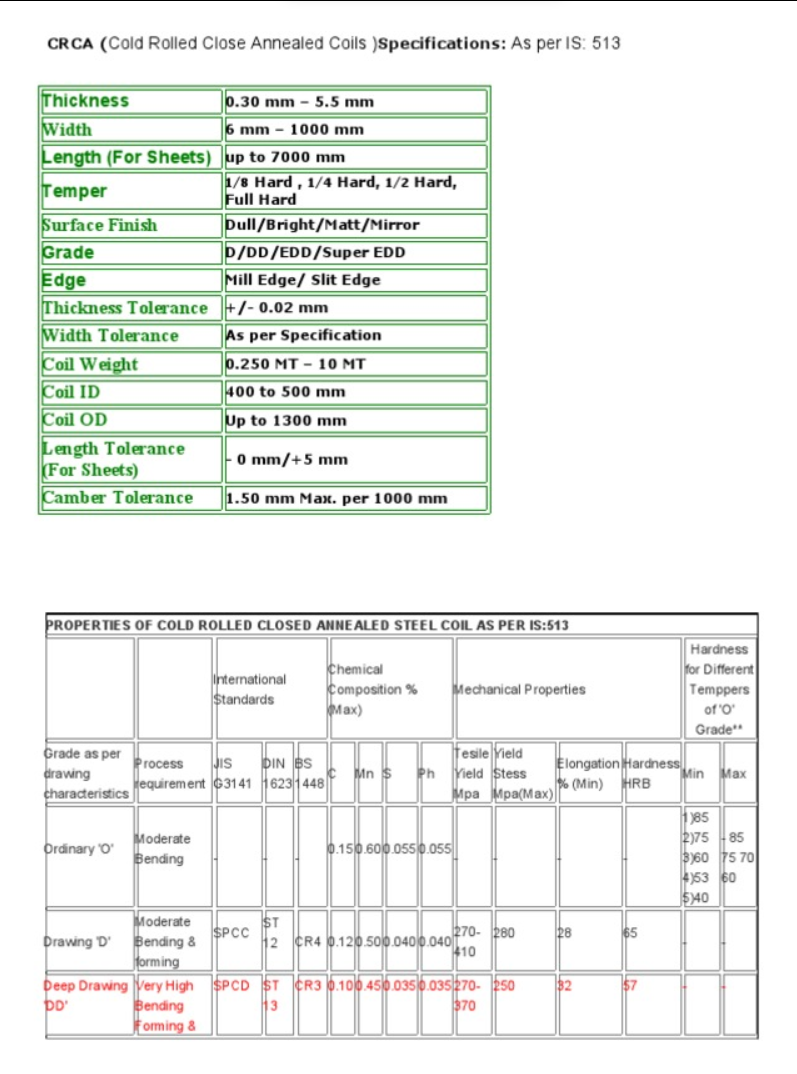
Note: the sheet thickness according to IS codes is too high. Normally, nobody makes CRCA sheets thicker than 1.8 mm. Labkafe lab furniture are generally made by CRCA sheets of up to 1.2 mm.
Application of CRCA Steel
Due to its high durability and strength, the CRCA material is eminently useful for the lightweight manufacturing industry, for making body and panels. You can find CRCA steel sheets in home furniture to space, even (and we’re not joking). You can use it in building bridge parts and building parts for its high strength. And for its great moldability and weldability, the automobile and furniture industry just loves CRCA steel. Most pressure and vessel manufacturing industries use it to build the outer bodies for their products. You will find it in airplanes as well as ships and boats. And yes, struts in space stations are built with similar CRCA steel as well!
CRCA Steel in Lab Furniture
The high moldability, internal strength, and durability of CRCA Steel sheet makes it an eminently good candidate for creating laboratory furniture and large paneled equipment. Since it is so strong, we can use it to make under-table supporting units, as well we can bend it into shape to create sectional supports for the workbenches.
- Note: find more information about how lab workbenches are made .
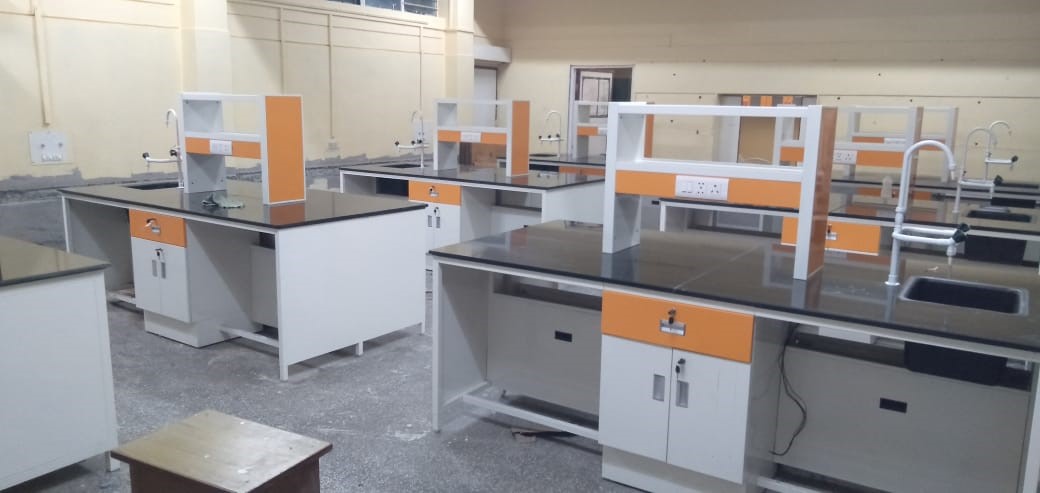
We know, lab workbenches do not get as much recognition as they should. When you think of a laboratory, you think of either a lot of glassware or high-tech gadgets ‒ but what are those things standing on? Lab workbenches form the very surface you need to work on, and therefore you need to make sure they are as reliable as possible. A damaged or corroded lab work surface is going to help nobody; instead, it may be a hazard.
This quality is easily brought to you by the capabilities of CRCA steel sheets. They are strong enough, but yet moldable to create shapes as necessary. While the stainless steel sheets of the same gauge are soft enough to bend by hand pressure only, CRCA sheets will not budge. It can hold immense weights, and the powder coating on it will last you a lifetime and protect the inner steel from the corrosive effects of various fumes we find in a laboratory.
Labkafe lab workbenches and support furniture like demo table or assistant’s table are all made from such high quality CRCA materials. The anti-corrosive powder coating does limit the number of available colors a little bit ‒ but then again, it is lab furniture, not a living room that needs to be decorated. Speaking of which, for decoration purposes we do have a lot of lab wallpapers and side sticker options, check them out!
Leave a Reply